Entre 2012 e 2018 foram registrados mais de 4 milhões de acidentes de trabalho em todo o Brasil, que envolveram desde fraturas até cortes e lacerações. Além disso, a cada três horas ocorre uma morte por acidente laboral no país. Como podemos ver, os números são altos e esses acidentes acontecem nos mais diferentes setores industriais. Nesse sentido, pensar na segurança do trabalho tornou-se algo vital para as empresas, de maneira a preservar a integridade e saúde de todas as pessoas que participam dos processos produtivos e/ou operam equipamentos.
A verdade é que os acidentes de trabalho também representam vários problemas e custos para as empresas: despesas com transporte, assistência médica e, por vezes, indenização do acidentado, diminuição da produtividade da equipe de trabalho devido ao impacto psicológico, despesas com reparos dos equipamentos danificados, custos jurídicos, atrasos no cronograma de produção e também prejuízos relativos à imagem da empresa responsável pelo acidente.
As Normas de Segurança
Para assegurar a saúde física e psicológica dos seus funcionários, é imprescindível que as organizações se pautem pelas Normas Regulamentadoras (NRs). Essas normas são um conjunto de requisitos e procedimentos relativos à segurança e medicina do trabalho, de observância obrigatória às empresas privadas, públicas e órgãos do governo. Ao todo, são 37 NRs, da NR-10 — que se refere à instalações e serviços com energia elétrica — até a NR-13, que diz respeito a caldeiras e vasos de pressão. Os conceitos apresentados na NR-12 são baseados na norma ABNT NBR 14153. Esta Norma brasileira tem como origem a antiga EN952-1, que teve seus conceitos atualizados, o que resultou no que conhecemos hoje como a ISO 13849.
A SMC, devido à sua abrangente área de atuação, tem a ISO 13849 como a norma internacional que rege as partes de comando relacionadas à segurança em máquinas e equipamentos. Assim, conceitualmente, também se adequa aos requisitos da nossa legislação. Além disso, existem as normas do tipo C, que são específicas para um determinado tipo de máquina. Alguns exemplos são a ISO 16092, partes 1 a 4, relacionadas a prensas mecânicas, hidráulicas e pneumáticas, e a ISO 10218, partes 1 e 2, relacionadas aos requisitos de segurança para robôs industriais.
Conheça mais sobre a NR-12
Para estar em conformidade com a NR-12, é necessário seguir um conjunto de procedimentos e requisitos, de maneira a garantir a segurança de todos os envolvidos no processo. Por isso, os sistemas pressurizados das máquinas devem possuir meios ou dispositivos destinados a garantir que:
- A pressão máxima de trabalho admissível nos circuitos não possa ser excedida;
- Quedas de pressão progressivas ou bruscas e perdas de pressão de vácuo não ofereçam riscos.
Além disso, a manutenção, inspeção, reparos, limpeza, ajuste e outras intervenções que se fizerem necessárias devem ser executadas por profissionais capacitados, qualificados ou legalmente habilitados, com as máquinas e equipamentos parados e com a adoção dos seguintes procedimentos:
- Isolamento e descarga de todas as fontes de energia das máquinas e equipamentos, de modo visível ou facilmente identificável por meio dos dispositivos de comando;
- Bloqueio mecânico e elétrico na posição “desligado” ou “fechado” de todos os dispositivos responsáveis pelo corte de energia, assim como a sinalização com cartão ou etiqueta de bloqueio contendo o horário e a data do mesmo, o motivo da manutenção e o nome do responsável.
5 passos para a segurança
Esses são os cinco passos da apreciação de risco para determinar o nível de performance da função de segurança.
1. Apreciação
A engenharia de segurança deve ser iniciada já no conceito e projeto do sistema. Perigos e riscos potenciais devem ser analisados conforme a ABNT NBR ISO 12100. Se não for possível a sua eliminação, os riscos devem ser reduzidos. Isto inclui avaliar todos os estados de operação do sistema: modo automático, de manutenção etc. A norma ANBT NBR ISO/TR 14121-2 pode ser utilizada como referência, pois é um guia prático para apreciação de riscos.
Entre as causas típicas de comportamentos perigosos em uma máquina, podemos destacar:
- Projeto inadequado ou modificação da lógica do sistema de controle;
- Defeito ou falha de um ou vários componentes do sistema de controle;
- Variação ou falha na fonte de alimentação do sistema de controle;
- Inadequada seleção, projeto e localização dos dispositivos de controle.
2. Redução de risco
Se não for possível eliminar todos os potenciais riscos na etapa número 1, é necessário tomar medidas adicionais. A ISO 12100 indica que são necessários três passos adicionais para a redução dos riscos, que devem ser seguidos em sequência:
- Projeto intrinsicamente seguro:
- Uso de orifícios fixos para redução de velocidade de atuadores;
- Risco do operador ficar preso é inexistente.
- Medidas técnicas de proteção:
- Sistemas relacionados à segurança;
- Controle de acesso;
- Detecção de pessoas;
- Grades de proteção.
- Informações e treinamento dos usuários:
- Sinalização e indicação dos perigos;
- Plano de manutenção;
- Treinamento e instruções de uso.
A NR12 segue conceitos similares direcionados para esta questão, entre os quais:
- O empregador deve adotar medidas de proteção para o trabalho em máquinas e equipamentos capazes de resguardar a saúde e a integridade física dos trabalhadores.
- São consideradas medidas de proteção a serem adotadas, nesta ordem de prioridade:
- Medidas de proteção coletiva;
- Medidas administrativas ou de organização do trabalho;
- Medidas de proteção individual.
3. O sistema de controle como componente para a redução de riscos
A ISO 12100 orienta que, quando as soluções relacionadas ao projeto são insuficientes para reduzir os riscos de forma adequada, devem ser utilizados dispositivos de proteção.
Os requisitos de performance dos componentes relacionados à segurança de um sistema de controle, para este tipo de equipamento de proteção, são indicados na ISO 13849, sendo aplicáveis para sistemas de controle pneumáticos, mecânicos, hidráulicos e eletrônicos. Os passos 4 e 5 esclarecem como determinar o nível de performance requerido (PLr), que serve como base para o nível de performance obtido (PL).
4. Determinação das funções de segurança da máquina
As funções de segurança de uma máquina devem ser especificadas. Isso inclui definir as funções necessárias, tais como retorno seguro para posição inicial, despressurização assegurada, prevenção contra partida inesperada, entre outras, e criar os diagramas para os componentes relacionados à segurança, assim como as reações requeridas em casos de falha.
Um nível de performance PL é determinado utilizando-se os gráficos de risco.
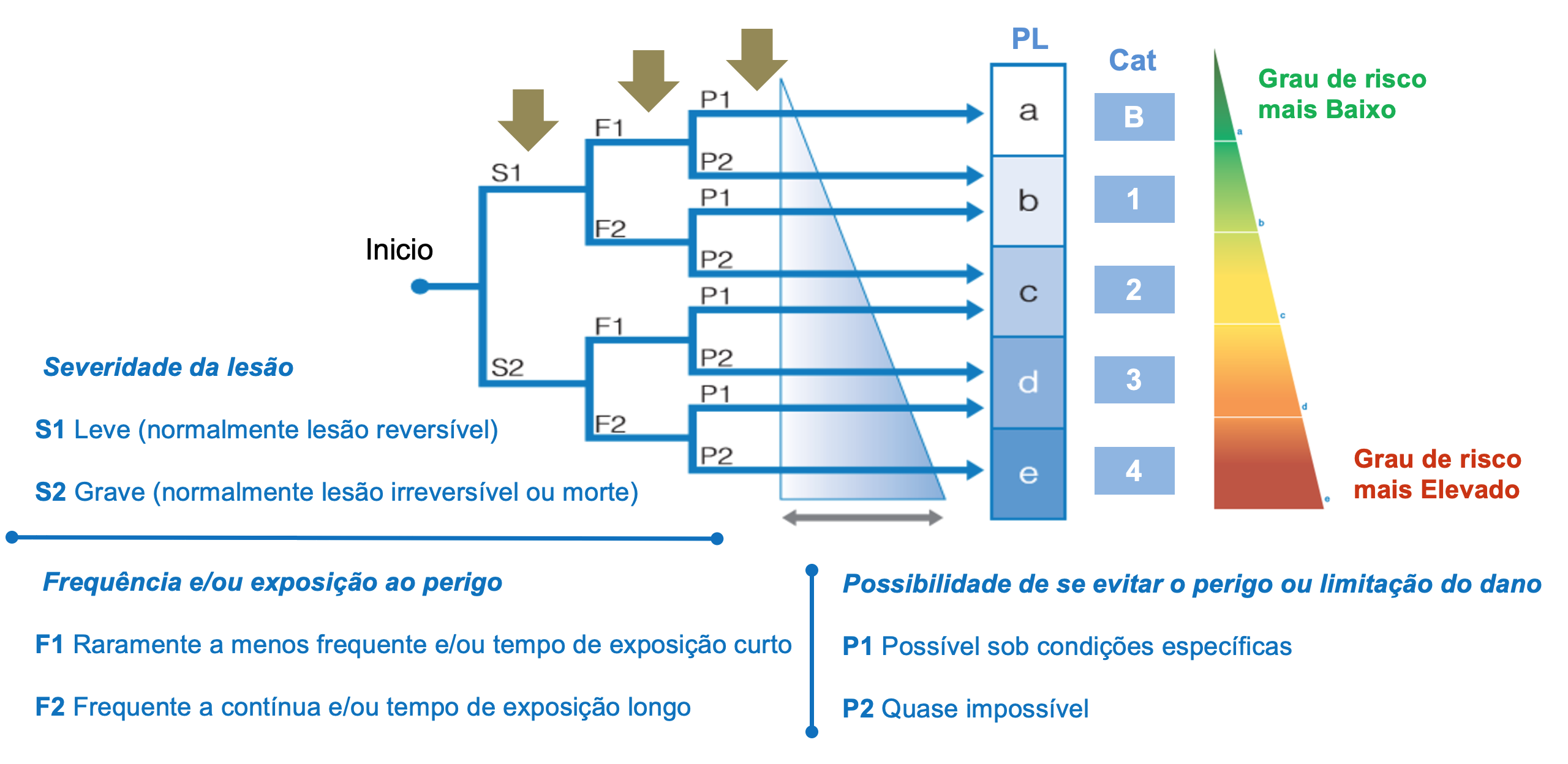
Gráfico de risco para determinação do PL, requerido para a função de segurança

Conheça, a seguir, alguns produtos da SMC relacionados com as funções de segurança das máquinas:
Parada Segura
Despressurização Segura
Proteção contra partidas inesperadas
5. Determinação do nível de performance atingido
Para avaliar o sistema relacionado à segurança, o nível de performance é determinado utilizando-se o seguinte:
- Estrutura (categorias);
- MTTFD (Mean Time To Failure Dangerous) – tempo médio até uma falha perigosa;
- DCavg – média de nível de cobertura de diagnóstico;
- CCF – falhas de causa comum;
- Resposta das funções de segurança quando em condição de falha;
- Capacidade de executar as funções de segurança quando em condições ambientais previsíveis.
É importante salientar que apenas profissionais habilitados podem emitir uma ART indicando que a máquina/equipamento está em conformidade com o que dita a NR12 e a ISO13849. Além disso, após a aprovação técnica não se deve proceder a quaisquer alterações do sistema sem consentimento do profissional de segurança.
Com operações no Brasil desde 1988 e estendendo-se a segmentos de atuação que vão desde o automobilístico até ao de mineração e siderurgia, a SMC vem se destacando pela sua constante preocupação com a segurança dos seus equipamentos. Por isso, a adoção de normas regulamentadoras direcionadas para a segurança laboral apresenta-se como uma consequência da qualidade dos seus sistemas e equipamentos.
Para mais informações, entre em contato conosco ou consulte o representante SMC da sua região.