Os fabricantes de máquinas têm se beneficiado bastante com a chegada das válvulas pneumáticas plug-in montadas em manifolds. Isso acontece porque este sistema permite que sejam montados conjuntos completos de válvulas em um local seguro e protegido da máquina. Com o uso de manifolds, tanto as ligações pneumáticas quanto as elétricas se tornam muito simples e compactas, podendo-se utilizar desde sistemas de fiação ponto a ponto, conectores múltiplos (DB-25), módulo de interface serial, ou até mesmo comunicação wireless.
No entanto, como acontece com a maioria dos avanços tecnológicos, pode haver algumas desvantagens nesse tipo de instalação, dependendo da aplicação. Uma delas gira em torno de ações para conservação de energia. A maioria dos circuitos inclui duas linhas de ar que se estendem da válvula até o atuador, uma para avanço e outra para retorno. Cada vez que a válvula alterna, o atuador se movimenta de um lado para o outro. Naturalmente, o tubo que os conecta também deve estar pressurizado. Esse volume de ar nessa tubulação é normalmente ignorado quando fazemos nossos cálculos de dimensionamento, mas nem sempre deve ser posto de lado.
O volume da tubulação não tem nenhuma função além de transportar o ar comprimido para o atuador mas, dependendo da aplicação, esses volumes podem ser significativos se medirmos o consumo.
Veja este exemplo:
Uma fábrica de embalagens tem caixas de papelão ondulado sendo erguidas no mezanino e transportadas até o piso principal, onde são enchidas, seladas e paletizadas. A caixa suspensa emprega gravidade para abaixar as caixas, mas incorpora uma série de paradas mecânicas subsequentes. Cada uma dessas paradas inclui dois cilindros pneumáticos para controlar um freio que libera a caixa quando necessário. Ao todo, são feitas quatro paradas no circuito, contabilizando o uso de oito atuadores e quatro válvulas.
As válvulas de controle direcional estão localizadas em um único manifold, formando um sistema limpo e compacto. No entanto, a distância do manifold ao atuador varia de 3 a 8 metros. Em operação, cada vez que uma válvula alterna, ela esgota o comprimento de um tubo e enche outro. Ao fazer as contas, vamos descobrir que o volume total do cilindro é de 280mm3 — ou seja, o volume dos tubos é mais da metade do volume dos atuadores. Grande parte da energia gerada pelo compressor está sendo usada apenas para encher as linhas de ar.
Podemos pensar que uma tubulação maior tende a ser melhor de qualquer forma e que tudo funcionará com mais eficiência. Mas aí é que está o erro: a tubulação maior pode dobrar o volume a ser preenchido sem adicionar benefício algum.
Outro problema visto frequentemente nas tubulações mais longas é o acúmulo de umidade, que acontece quando há excesso de ar entre a válvula e o atuador. Quando esse acúmulo de condensado ocorre próximo ao atuador, pode invadir o equipamento e reduzir a sua vida útil.
Qual a solução?
A melhor forma de prevenir estas questões é se certificar que a montagem das válvulas seja feita sempre o mais próximo possível dos atuadores, fazendo com que se perca menos ar comprimido no preenchimento da tubulação.
Para aquelas instalações em que não for necessário o uso de manifolds, existem cilindros que já possuem válvula incorporada, o que reduz significativamente o volume de ar utilizado em seu acionamento.
As linhas elétricas terão de ser estendidas de forma independente de cada válvula, mas se isso for feito em baixa tensão e baixa potência, o processo não será tão difícil. Além disso, a resposta em sistemas elétricos não terá alteração de tempo, mas há uma melhora considerável nas respostas em sistemas pneumáticos.
Conheça alguns componentes SMC que colaboram para reduzir o volume excessivo
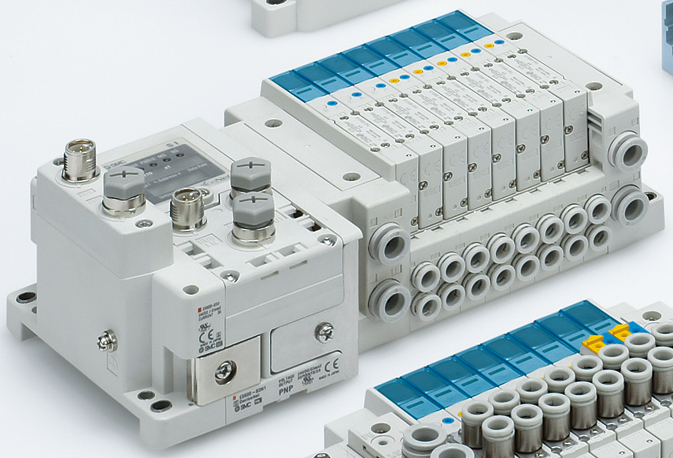
Manifold SY
Benefícios: Instalação mais simples e compacta; facilidade na identificação, organização e estética.
Cuidados: Instalar o mais próximo possível dos atuadores.

Atuador com válvula incorporada
Benefícios: Menor volume de ar entre válvula e atuador, redução da quantidade de tubos utilizados
Cuidados: O acesso à válvula pode ser mais difícil, dependendo da instalação.
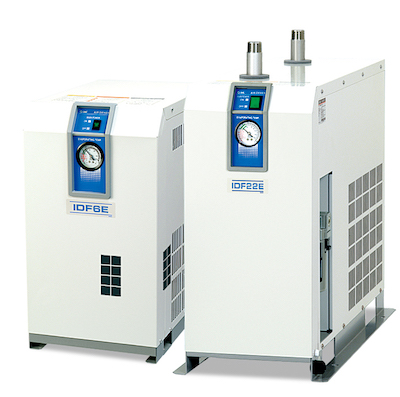
Secador de ar
Benefícios: Menos umidade, menor formação de condensado na tubulação, maior vida útil dos componentes pneumáticos.
Por essas razões, devemos permanecer atentos aos custos de ar comprimido, e constantemente avaliar o melhor local para instalação das válvulas, de maneira que a tubulação não se prolongue desnecessariamente. Além disso, para evitar formação e acúmulo de condensados na tubulação, é necessário tratar adequadamente o ar comprimido desde a geração até a utilização, com o uso de filtros e secadores de ar.
No entanto, lidar com questões como essa da forma como descrito neste artigo oferece uma solução mais simples, com pouco custo adicional. Veja na coluna ao lado alguns produtos que podem ajudá-lo nesse desafio. O que era um problema “inconsequente” pode se transformar em uma economia significativa.
Para mais informações, entre em contato conosco ou consulte o representante SMC da sua região.